アナログ対 デジタルガルバノメータ技術– 紹介
Authors: Matthew Tedford, Jeremy Berke, Ali Golabchi, Malte Hemmerich要約
When designing a new laser application with beam deflection units, most engineers will choose the optical design (mirror size, coatings, mirror material) with great care. This makes sense as the effective focal length, spot size and the power handling the system are all crucial. However, choosing the right galvanometer technology is just as important for the overall achievable performance of the application. In this white paper, we discuss the advantages and disadvantages of analog galvanometers and servo units and, in particular, hybrid solutions using digital servo technology with analog galvanometers. Influences of the respective technology on achievable speeds, accuracies and integration hurdles are examined.ガルバノメーター - デジタル対 アナログ
Galvanometers (galvos) at their heart, are limited rotation DC motors with a precision position detector (PD) at one end and, in this context, a mirror at the other. While the size and construction of the motor may vary, and will impact the performance of the galvo, the position detector is the key component of the device. Over the years, galvos have used capacitive sensors, optical sensors, and encoders to determine the position of the rotor shaft and the opposing mirror. The most common PD’s in the modern era are optical sensors and encoders which will be the two feedback mechanisms focused on for this section of the paper. Optical sensors for position detectors have been used in galvos since the early 2000’s. See Figure 1 for example. This PD is commonly found in Novanta’s Cambridge Technology 62xxK and 83xxK series of galvanometers. The rotor shaft of the motor has the butterfly attached to it and as the rotor turns, the butterfly covers and uncovers parts of the photocells. The photocells in turn generate two currents on the scale of microamps that are sent back to the servo board which then converts the current to a voltage to determine the angular position of the rotor. This, coupled with the rest of the control loop, ensures precise and stable operation of the galvo while following the commands provided by the servo board.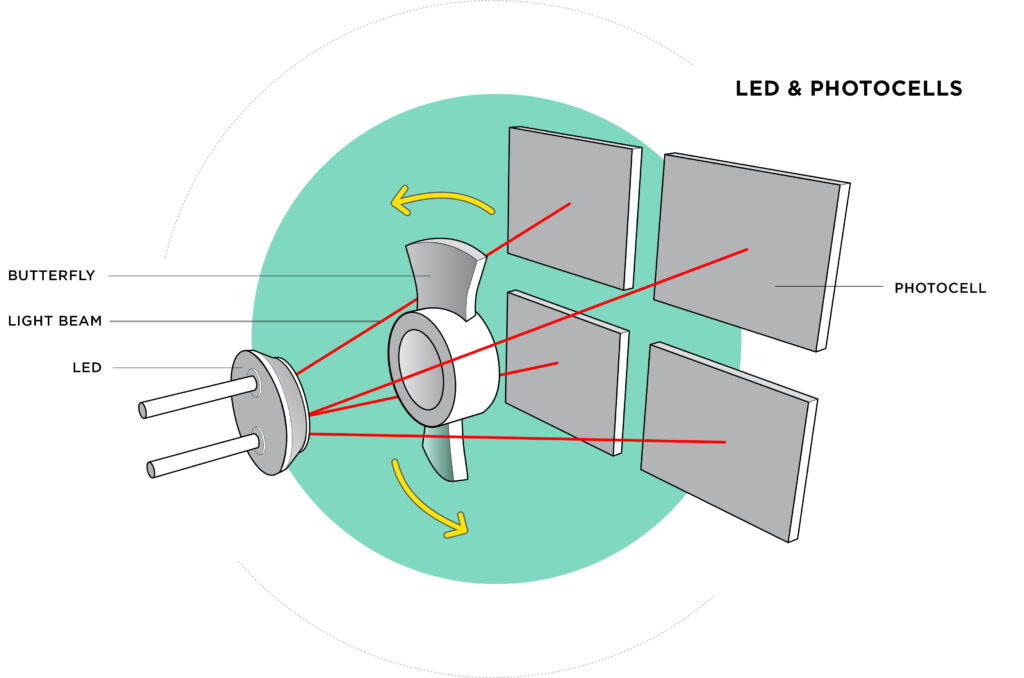
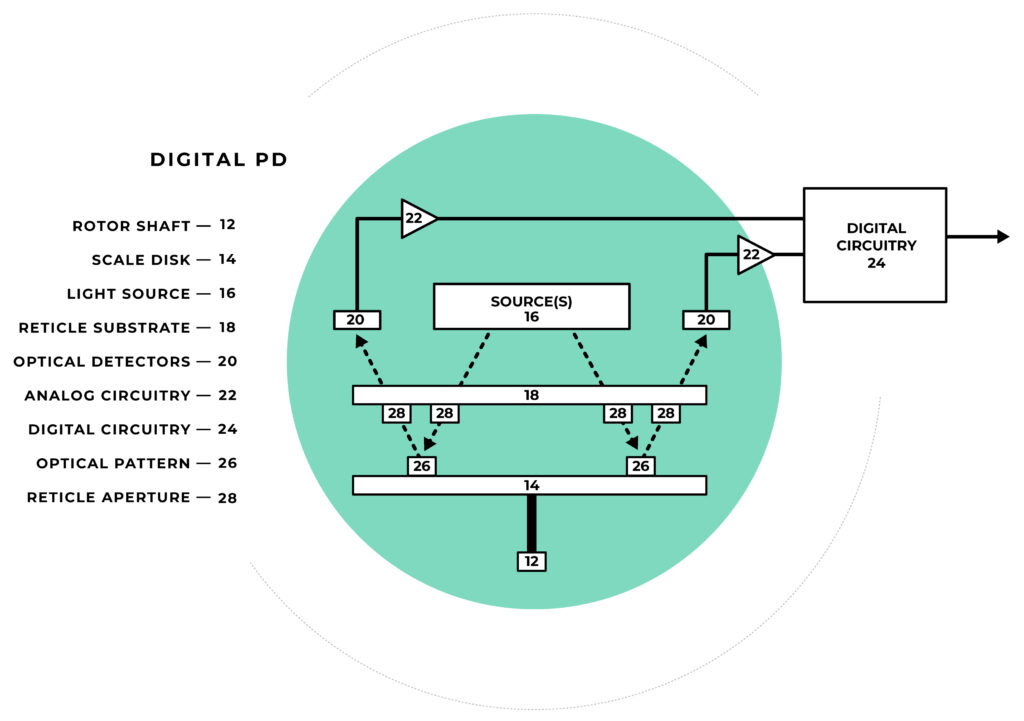
サーボ– アナログ 対 デジタル
The control loop in analog servos use a large number of variable resistors to tune the galvo performance. This fact requires an individual tuning process for each servo-galvo pair which makes any tuning changes or replacements of individual components outside of the factory very difficult. Also, because the system uses potentiometers to set the tuning terms, there isn’t a way to pass the values up to a system control to do predictive control. Digital based servos on the other hand are flexible and can provide higher accuracy. Because the control loop for these servos exists in firmware, they can be changed and adapted at any point in their lifespan without the need of additional hardware. Even remote adaption of an existing digital servo to a new galvo, or vice-versa, can be achieved. While analog servos typically uses position, velocity, and current feedback signals to control the galvo, digital servos can also use feedforward, modeling, and much more to allow for a higher level of control and even pass the values to the upper-level system controller for use in predictive control like Novanta’s ScanPack. ScanPack prioritizes accuracy and quality based upon the needs of the application. Vectors, circles, points, and spirals can all be customized to a high degree for peak performance.ハイブリッドシステム - アナログガルボとデジタルサーボ
There is a wide range of applications that do not require the highest drift-performance and accuracy that digital galvos can provide but would benefit from the re-tunability and flexibility of a digital servo. Thus, it is a rather common desire to combine the advantages of the cost effective and rugged design of analog galvos with the perks that come with a digital servo. If a standard 62xxK/83xxK analog galvo meets the performance needs of an application and the application values the flexibility offered by a digital servo, then Novanta’s soon-to-be-released Versia scan head or a component-based solution with a digital servo can be the best answer. As outlined in the previous section talking about servos, there is a lot of value that a digital servo can bring to an application. A digital servo gives an extra level of field serviceability, flexibility, and control to the analog galvos through ScanPack. One of these advantages is the ability to decouple the servo from the galvo. This means that when it comes to field service, a technician may only need to replace a galvo or servo instead of the entire set and re-tuning the system can be performed in the field, whereas the analog system would have to be returned to the factory. This greatly reduces the material cost of a repair and reduces the time on site for a technician or the overall time it can take to repair a system. Another advantage of a digital servo is the level of flexibility it provides during initial integration. As mentioned previously a digital servo potentially allows a customer to decouple the serial numbers, thus increasing the late-stage configurability of a system. As an example, let’s assume there is a production line that manufactures 8 and 10mm marking systems where the servos are in a machine enclosure. With an analog galvo and servo, care needs to be taken to ensure that the galvo-servo pair never gets separated. This may limit the way material can flow through a production line. Whereas with a digital servo, the control cabinet could be built on one line, and the scan heads could be built on another, and it wouldn’t be until they were being built into a final machine that they’d be paired and tuned. Also, by pairing the analog galvos with the digital servos, the turning terms move from the analog world of potentiometers to the digital realm. This means that the values of the tuning terms can be passed up to the controller of the system, such as Novanta’s ScanMaster Controller, and be used for predictive control which allows an application to move to the next level of accuracy and quality for an application. The job creator can now define the speed at which the galvos enter and exit a vector or corner, eliminating laser pulse stack up. The developer also gets greater control over circles, spirals, and points. To provide a more specific example on the predictive control ScanPack provides, most servos tend to use a state feedback control scheme, which can impact the performance of marking small circles if the system bandwidth isn’t high enough. see Figure 3 . The tear drop shape caused by the feedback control and low bandwidth can be corrected by increasing the bandwidth (i.e., faster tune), but doing so would increase the noise of the system.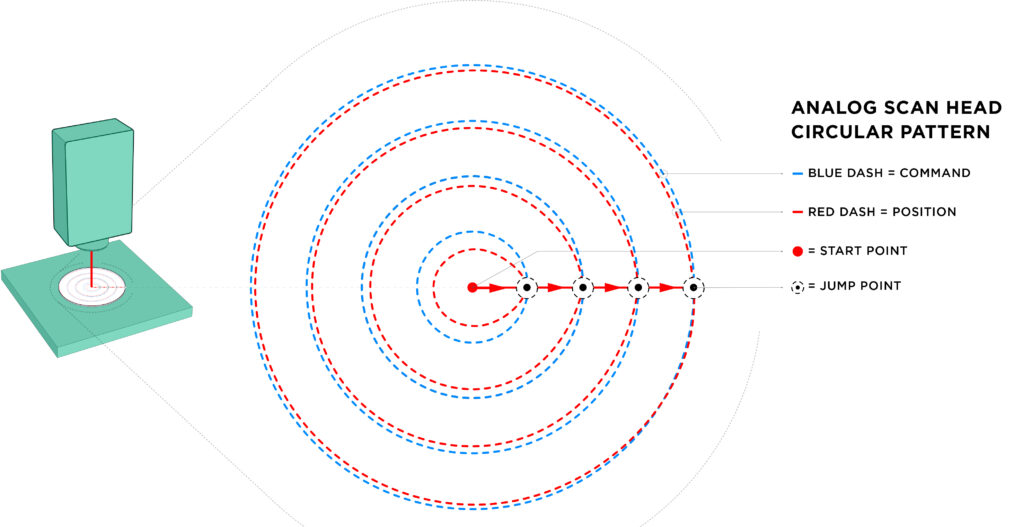
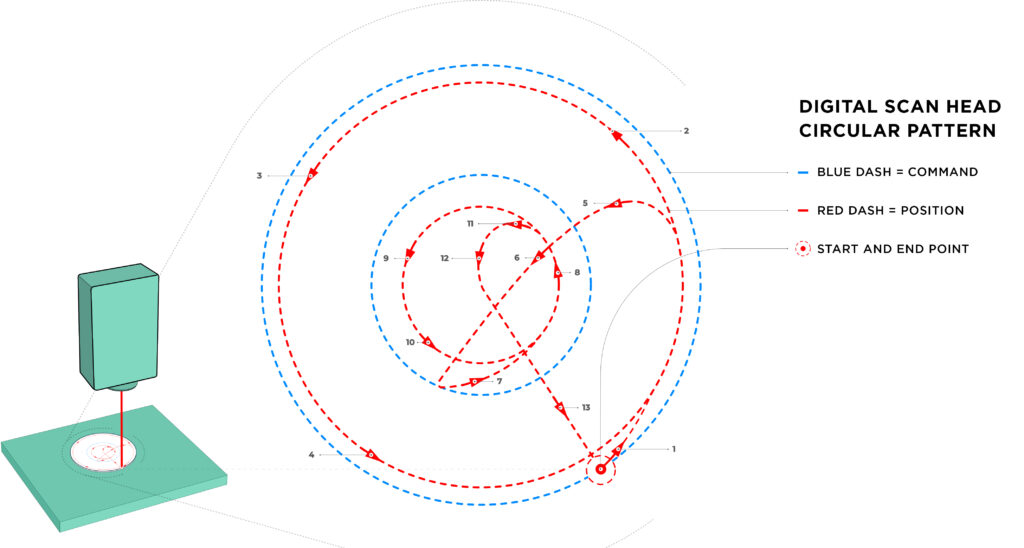
結論
要約すると、アナログとデジタルのガルバノメーターおよびサーボの3つの組み合わせは、アプリケーションのニーズに応じて利点を提供します。 これらの利点は、表 1で簡単に比較するためにまとめられています。
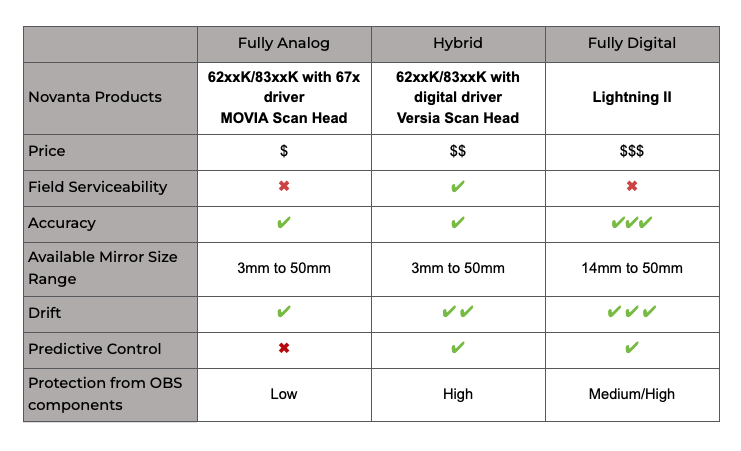